Happy New Year 2023 :) I can’t believe this blog has 10 years!
Today, let’s talk about a few questions that I get all the time:
- What does linearity means?
- What is the difference with nonlinear simulation?
- When do you actually need nonlinear simulation?
Video:
Let’s talk first about the concept of linearity
Linear static is the most basic type of simulation that is performed every day by engineers and designers.
The concept of linearity is close to the concept of proportionality.
When you apply a force on a simulation model and you calculate some results such as displacements, stresses and strains with a linear simulation, you are only calculating the results from that unique force value, but you could obtain results for an infinite number of forces.
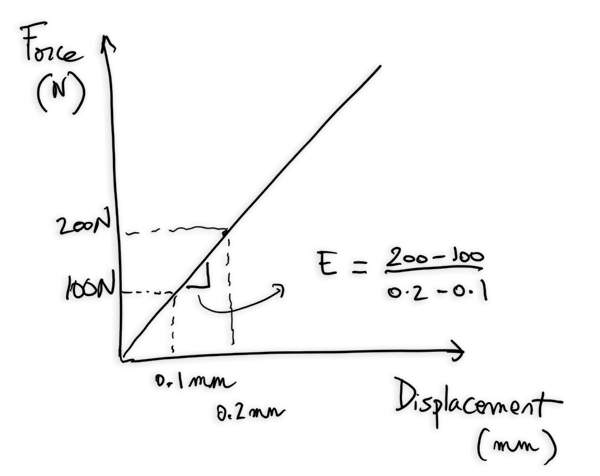
What I mean is that if you multiply the input force by a coefficient, then the results will also be multiplied by the same coefficient, that’s what linearity means.
There is a proportionality relation between the input force and the results you get.
Why does this happen?
When we do a linear simulation, we are making a few important assumptions, and especially on the material model that is used to approximate the real world material
Related Articles:
What is a material model?
The material in reality is never just a big uniform block of matter, it has a complex microscopic structure with a lot of imperfections.
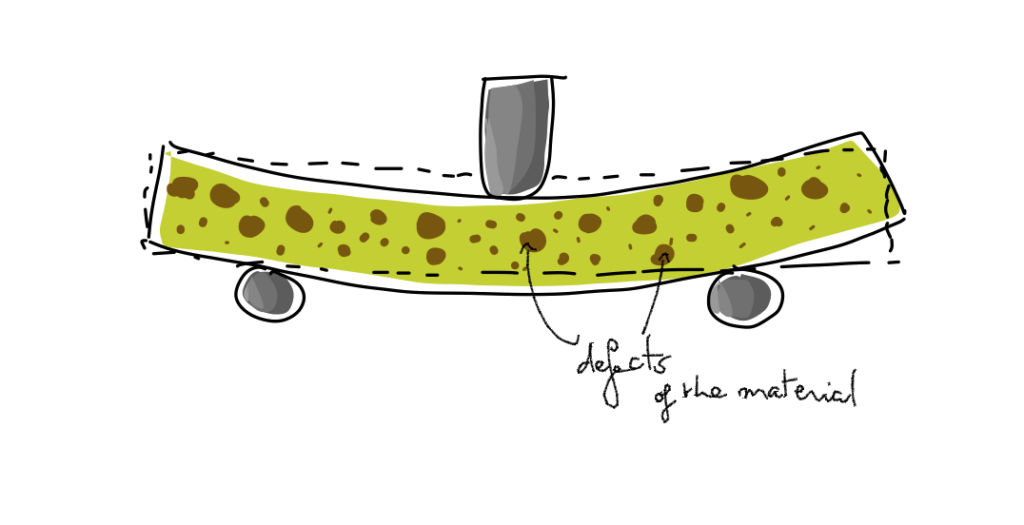
However, some materials like steels for example can be approximated by such an isotropic block of mater and when we decide to stay within small deformations, we can can define this material as a relation between stress and strain.
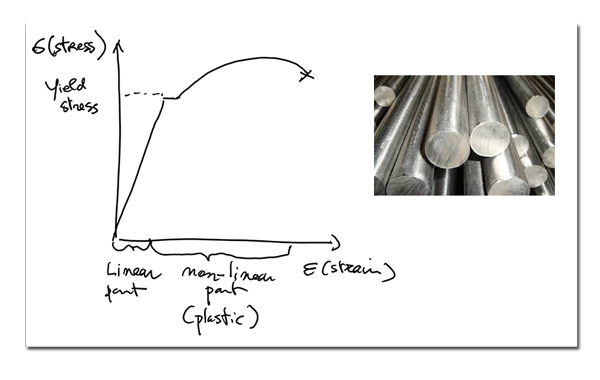
This is called an elastic material model and this is what allows us to define a linear relation between stresses and strains.
This relation between stress and strain, called Hooke’s law, is defined by only 2 coefficients: The Young’s modulus and the Poisson’s ratio.
Related articles:
When can I use linear simulation?
If your simulation purpose is to analyse several design variations to compare the difference between the designs and you stay within small deformations at all times, then you can use safely linear simulation.
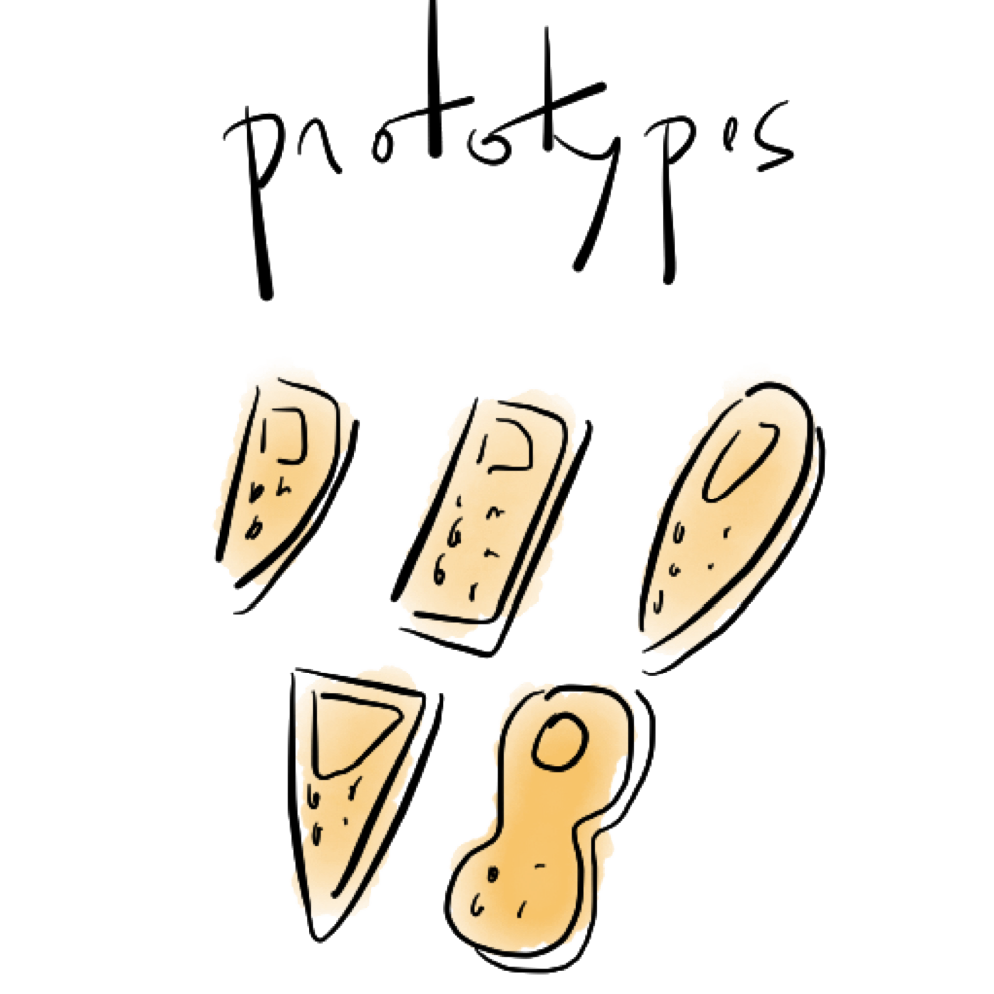
Linear simulation will calculate for you a safety factor that will give you an indication about how «safe » your design is how it compares to other designs.
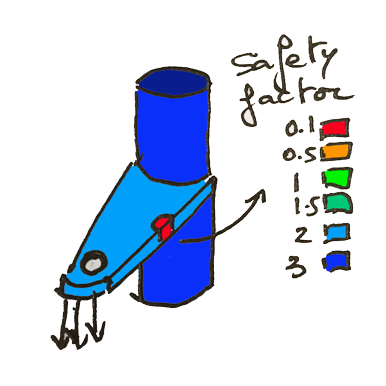
Nevertheless, if you find out that your stresses, displacements are getting larger than they should, you either have something very wrong in your simulation settings or you will need to switch to a nonlinear simulation.
Related articles:
When do I need to use nonlinear simulation?
Well, the first reason to use nonlinear simulation would be if you can’t stay in small deformations anymore.
If you plan to apply a large load and you really want to simulate what happens at the failure, then the assumptions we made for the linear simulation aren’t valid anymore and we need to switch to a nonlinear simulation that will use nonlinear material models.

That’s when things become more complicated because then you have to consider a bunch of new things that you didn’t need in a linear simulation such as:
- Nonlinear Material Models
- Nonlinear contacts
- Large Deformations
Also nonlinear simulation is not as immediate as linear simulation.
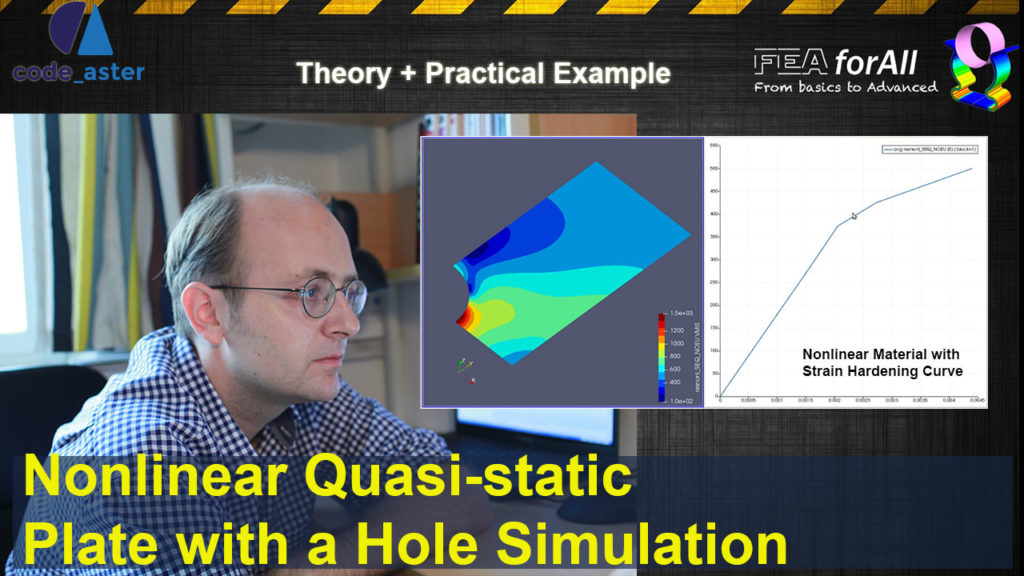
If I simplify, a linear simulation comes back to calculating the inversion of a huge matrix with (sometimes) millions of degrees of freedom, so it is a big calculation, but with a computer, that’s something you can solve in one iteration (Methods like LU decomposition can be used to invert matrices pretty efficiently by direct numerical solvers).
A nonlinear simulation introduces the concept of iterations and convergence. to get a solution, you have to compute a series of matrix inversions, each of them with a certain level of error that can lead to convergence or divergence of the solution based on the set up of your simulation model.
That’s why it takes much more time and experience to:
- Build a correct model that will lead to convergence
- Get results close to reality using the proper nonlinear material or contact model
Here’s an interesting video if you want to dive a bit deeper into the topic:
Related articles:
- Nonlinear Explicit Structural Analysis
- [Salome Meca Tutorial] Leaf Spring Nonlinear Material and Contact FEA Simulation – Part 1
That’s all for today guys, I hope it was useful and that you now know the difference between a linear and a nonlinear simulation.
Let me know if you have some questions, I am always glad to answer them
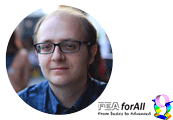
Cyprien “Helping you to get started with nonlinear simulation” Rusu
I mis tutorials of pumps simulations in Open Foam. The CFD flow analyses, simulations and calculation me the trust what I have designed to meet the expecation.
I make my designs in CFTurbo.
Regards,
Hans Hofmeijer.