In my previous article, I asked to my newsletter subscribers 2 questions to see who knew how to perform a dynamic analysis of the following marine refrigeration machine:
The questions were:
Question 1:
What steps would you take to identify the main vibration characteristics of the marine refrigeration machine in the previous image?
Question 2:
What would be the main challenges you can expect to meet in such a complex FEA analysis?
Ok, now, take the time to think, don’t read the answer below that line…
Answer:
Congratulation, Erkan Talay, you nailed perfectly the answers to the simulation problem! I am impressed.

Let’s analyse Erkan’s answer together…
Do you see the « key foundational pieces of knowledge » I was talking about?
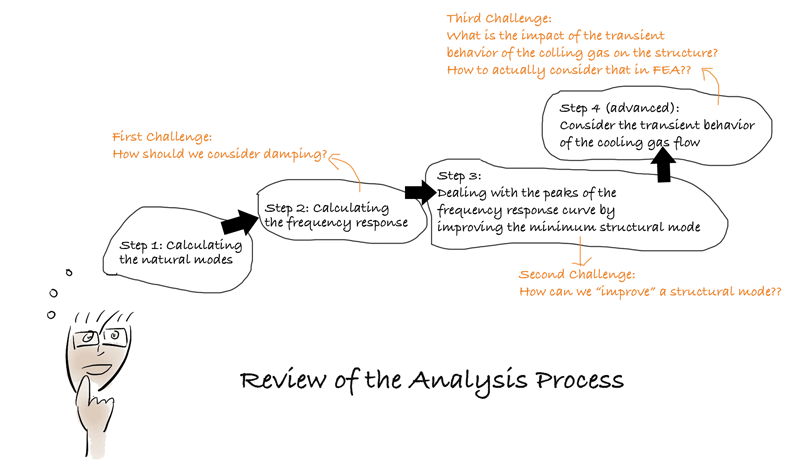

Step 1: Calculating the natural modes.
A modal analysis can help us here to identify the modes of vibration of this system.
Read more about modal analysis here
Step 2: Calculating the frequency response
A modal analysis only gives us the natural frequencies of vibrations, but it doesn’t provide the actual dynamic response to a given dynamic excitation. That’s when we need to use frequency response analysis.
Read more about frequency response analysis
Step 3: Dealing with the peaks of the frequency response curve by improving the minimum structural mode
In FEA, what is really important is the data you actually get, because data is what tells you where you can improve your model or where you have a problem in your design.
Now… you need of course to have accurate results in order to be able to make some conclusions… and this is not necessarily obvious…
Read more about the dangers of bad accuracy in FEA results
Step 4: Consider the transient behaviour of the cooling gas flow
Now we are getting to the advanced stuff ;-)
Simulating the flow inside the machinery along with temperature can be really challenging.
First you have to understand heat transfer, secondly, you have to understand CFD (Computational Fluid dynamics).
Read more about the physics of heat transfer here
The thing is…
If you want to simulate anything more complex than a plate or a beam, chances are that you will need this « key foundational knowledge »… along with experience & practice of course
Yes, you will have to learn and refine your skills to understand all the details. But once you do, everything will become easier ;-)
The other good news is that you don’t need to start right away with such a complex model.
In fact, whenever I start to analyse something rather complex, I like to simplify the model a maximum in order to be able to nail down the most important choices you’ll have to do right from the start.
Want to know more about dynamic analysis?
Take the pill and follow the white rabbit into the rabbit hole ;-)

Read those articles to understand better dynamic analysis:
Read my article explaining about modal analysis
Read my article explaining about frequency response analysis
Read my article explaining the difference between steady state and transient response
//////////////////////////////////////////////////////////////////
I really want to contribute and help engineers (and students) who are new to FEA to understand basic concepts better and faster!
If you like this article, there are 3 things you can do for me:
1- Help me to share this article on Linkedin, facebook, twitter or in your habitual forum to help more people understand those basic concepts better.
2- Let me know in the comments what you learned from it and what you would like to learn even further so I can write more on the topic.
3- Join the newsletter and I’ll send you everything I write (and much more) by email!
Thank you for reading!
–Cyprien “Understanding is dynamic” Rusu ;-)
This one is your best article
Hello Sir,
Hope you are doing Fine. I would like to discuss my query about cylindrical support. I am doing a simulation of the clutch assembly where a clutch assembly is mounted with the shaft and shaft is rotated by a gear. There are two bearing which connects and hold the shaft. I just want to confirm at the place of bearing, I have taken cylindrical support and which option I should keep free or fixed from radial, axial, and tangential. I have keep all three options as fixed. I also want to know, how to add oil temperature(120 Celcius) on the clutch plates in the simulation. I have taken 120 degree celcius environment temperature on the plats in the clutch assembly and rest of the parts are at normal temperature.I am performing the structural transient analysis and there are four loads: rotational velocity in rpm, torque, springs forces and gravity. Now, i would like to know this FEA setup is fine for transient structural analysis. I am I am eagerly waiting your response.
Thanking you
Thanks a Ton for this article. I am looking forward to have more such articles.