In the last article, I talked about composites and where they come from… now let’s talk a bit about one of the main reason we use composites… Their strength !
Composite Materials are lighter and stronger, that’s why they are great!
Why don’t we use composites everywhere then?
The reason is simple, they are expensive and difficult to manufacture…
Quantifying the strength of composite materials
One problem that arises is that there are various scales of mechanical system… small and very small (car parts, electronic parts…) and very large (Mining engine, plane structure…)
So how can we classify the strength if the loads applied are so different in terms of scale?
That’s where specific strength (strength normalised by the density of the material) and specific modulus (modulus normalised by density) are coming handy.
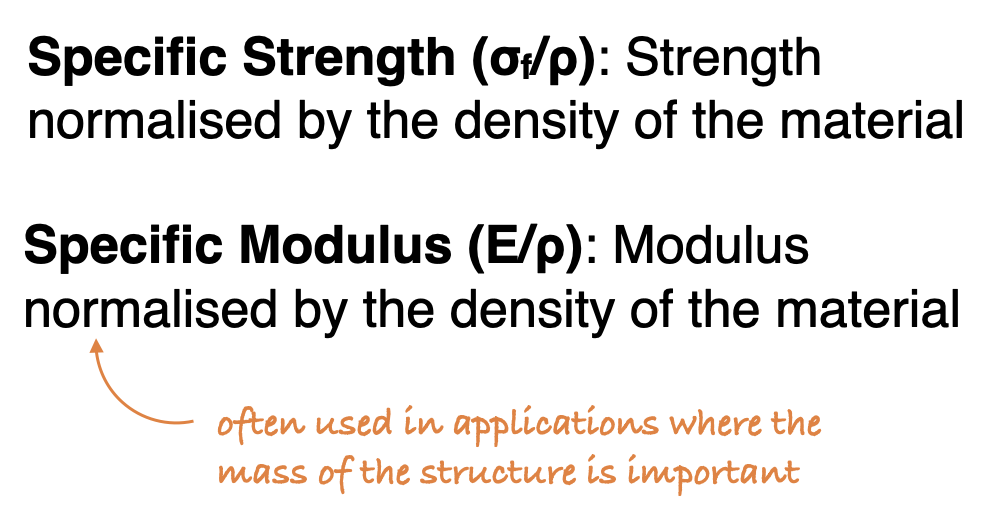
Specific Strength is basically a measure of the capability of a unit mass of a material to support structural loads.
This is often used in applications where the mass of the structure is important, e.g. transportation and aerospace applications.
Now let’s look at this figure which shows in a concise manner the different kind of composites ordered by their specific strength
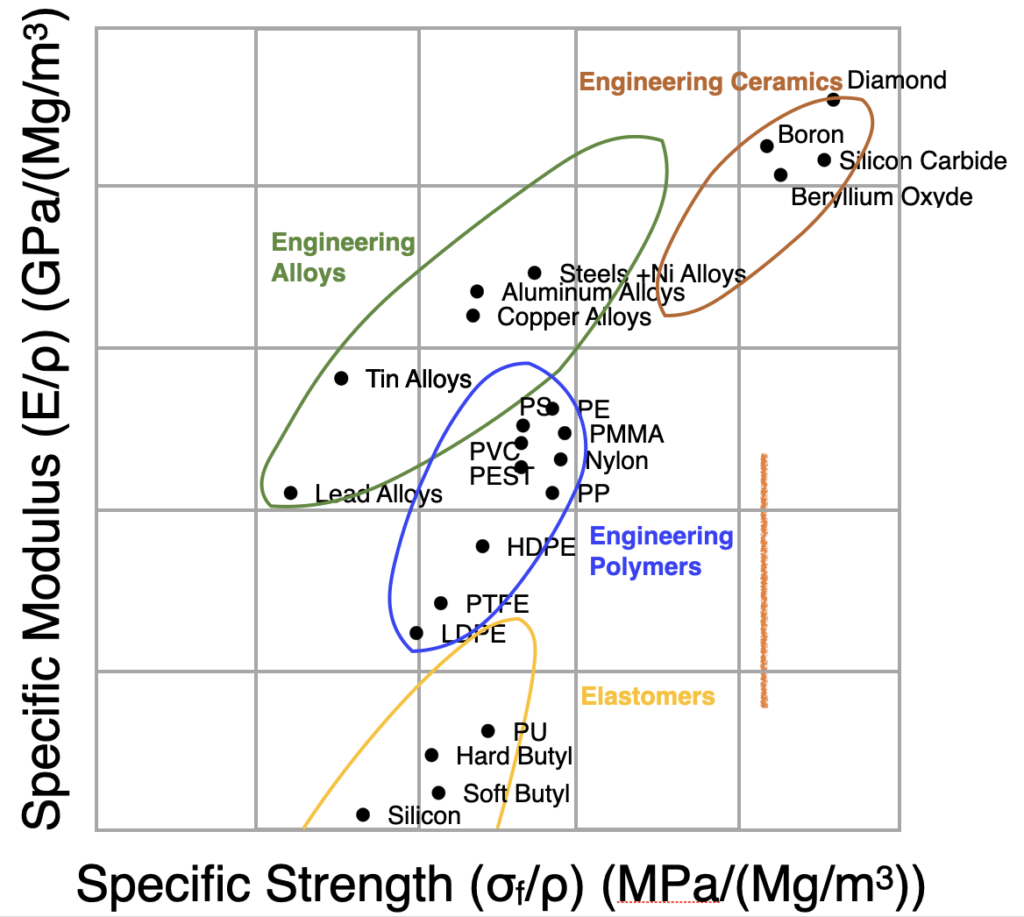
Let’s now talk about the different types of composites in this figure
Engineering Ceramics
Engineering ceramics are a class of advanced materials known for their exceptional hardness, thermal stability, and resistance to wear, corrosion, and high temperatures.

Boron carbide, often called “black diamond,” is one of the hardest known materials after diamond and cubic boron nitride, featuring high hardness, low density, and chemical stability, making it ideal for lightweight armor, abrasive tools, and wear-resistant components.
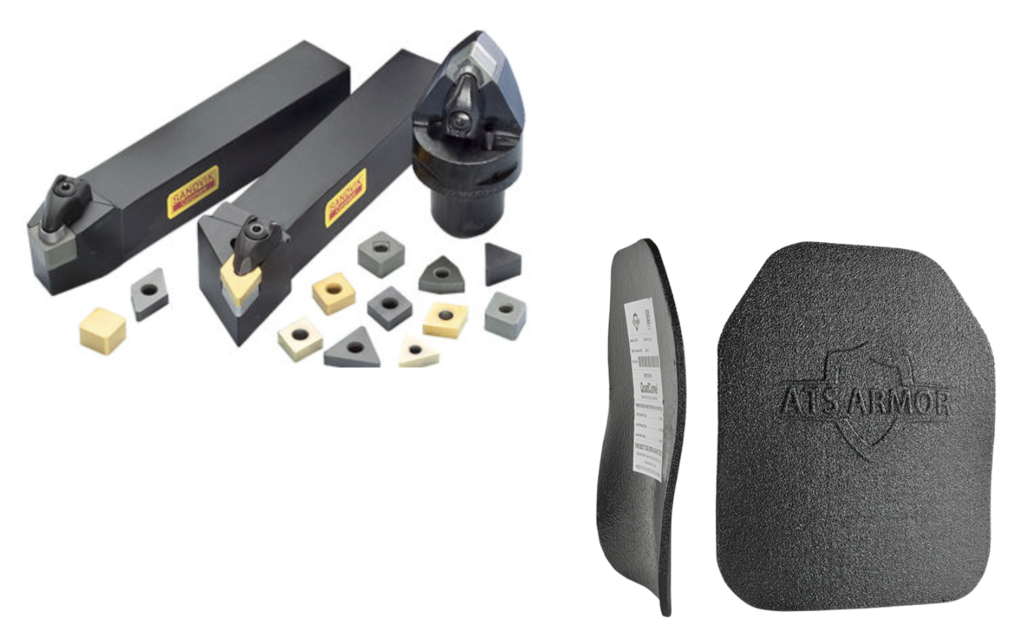
Diamond, especially in its polycrystalline ceramic form, combines unmatched hardness with excellent thermal conductivity, finding use in cutting, grinding, and advanced electronics due to its mechanical and thermal properties.
Silicon carbide stands out for its high strength, hardness, oxidation resistance, and chemical durability, serving in high-temperature structural components, mechanical seals, and heat exchangers.
Beryllium oxide is prized for its outstanding thermal conductivity and electrical insulation, alongside mechanical robustness and low density, making it a preferred material in electronics, aerospace, and high-performance heat dissipation systems.
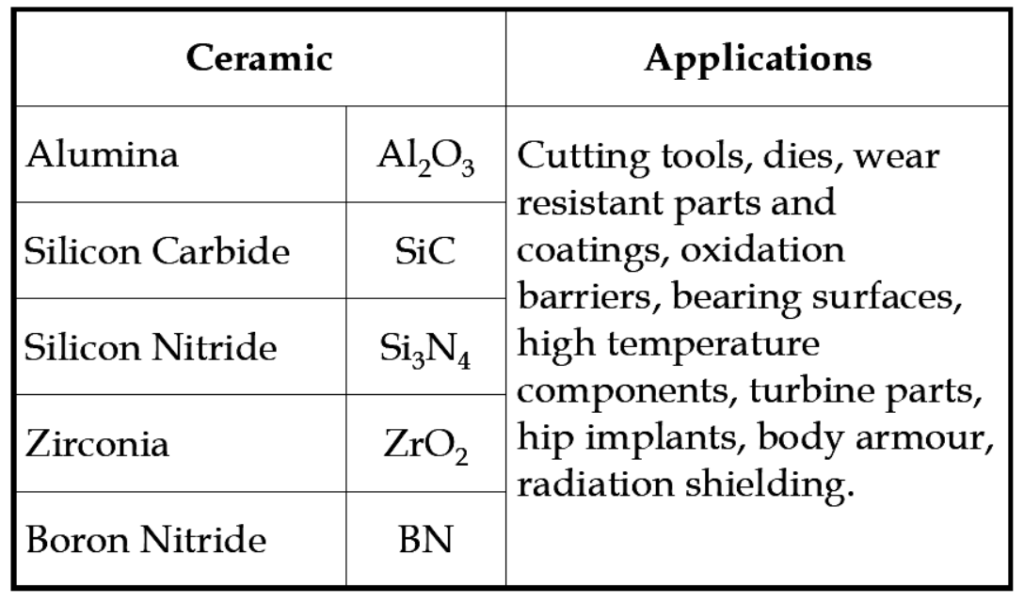
Engineering Alloys
Engineering alloys are materials created by combining a primary metal with other metallic or non-metallic elements to enhance specific properties such as strength, durability, corrosion resistance, and workability.
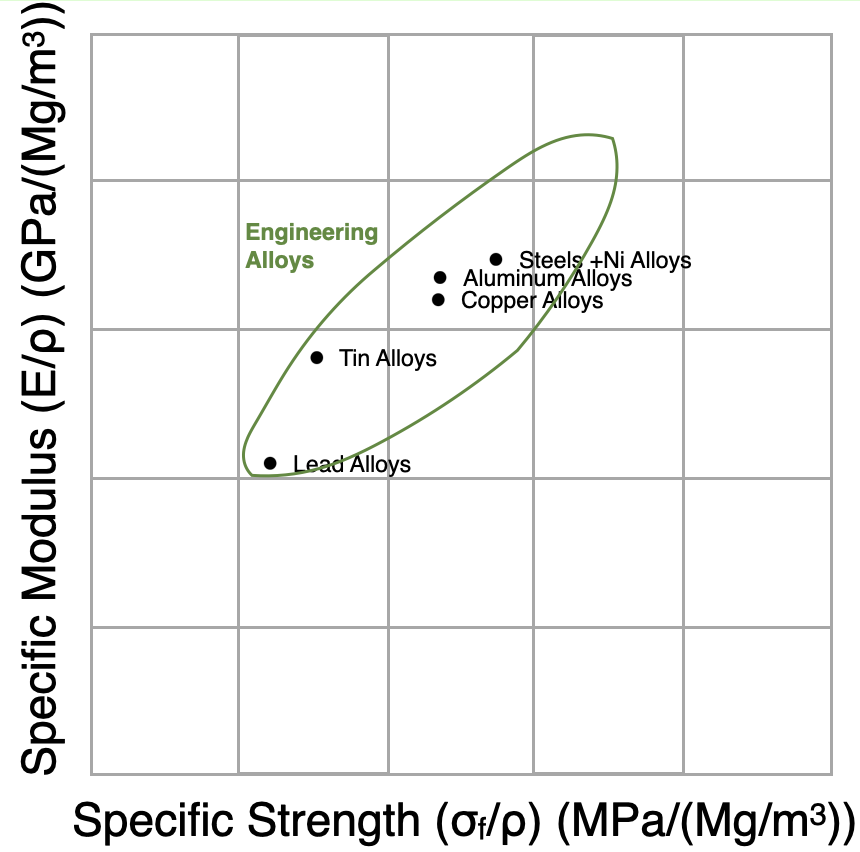
Steel alloys, for example, are based on iron and carbon but often include elements like chromium, nickel, or molybdenum to improve hardness, toughness, and resistance to wear and corrosion, making them essential for structural, automotive, and aerospace applications.
Aluminum alloys are valued for their low density, high strength-to-weight ratio, and corrosion resistance, making them ideal for transportation and aerospace industries.
Copper alloys, including brass and bronze, offer excellent electrical and thermal conductivity, as well as good corrosion resistance, and are widely used in electrical, plumbing, and marine applications.
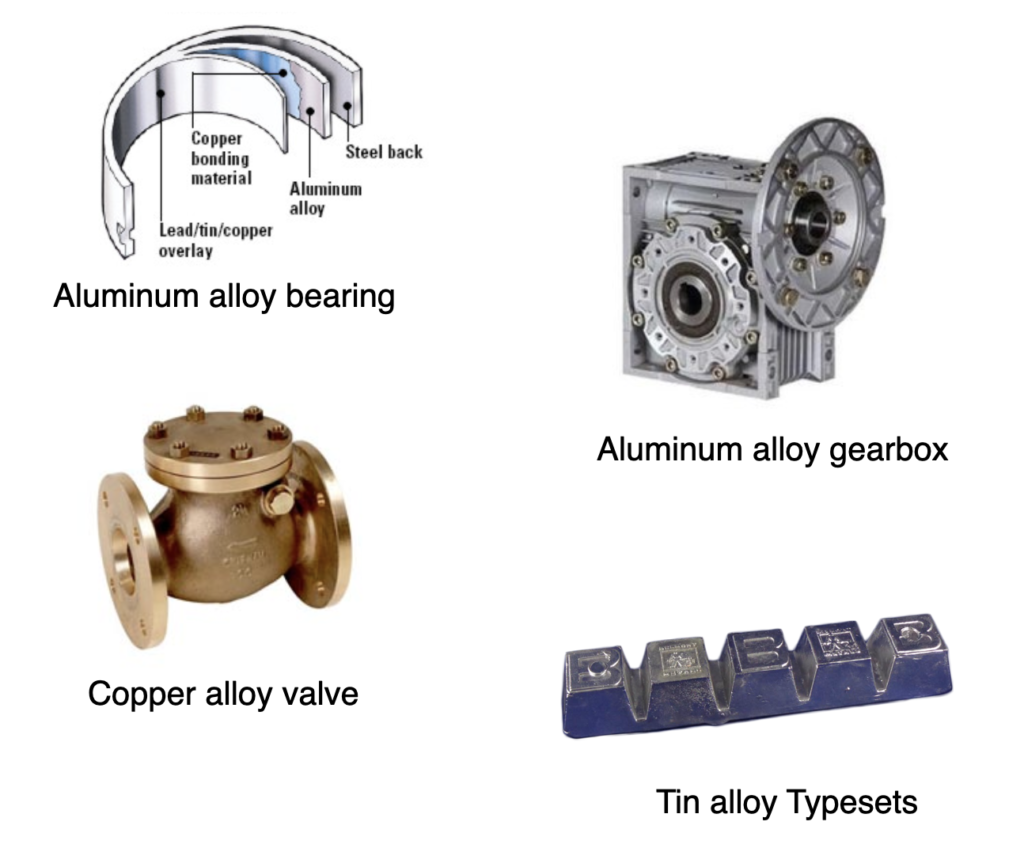
Tin alloys, such as bronze (copper and tin) and various soldering materials, are known for their low melting points and resistance to corrosion, making them suitable for bearings, electrical connections, and decorative items
Engineering Polymers
Engineering polymers are a diverse group of synthetic materials designed to meet specific performance requirements across a wide range of industries.
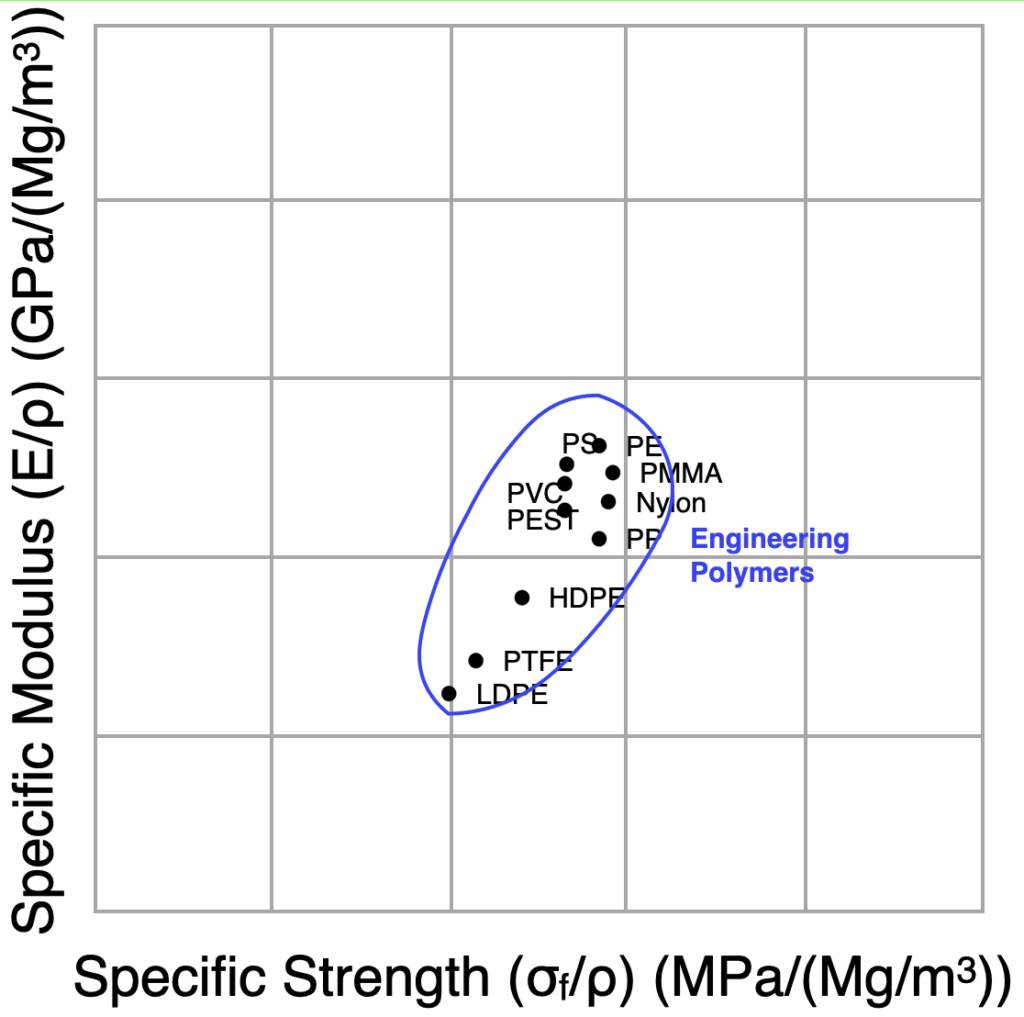
Examples include polyethylene (PE), known for its flexibility, chemical resistance, and availability in both high-density (HDPE) and low-density (LDPE) forms for applications from packaging to piping;
Polypropylene (PP), valued for its lightweight, chemical resistance, and toughness, making it ideal for automotive and consumer goods;
Polyamide (PA, or nylon), which offers high strength, durability, and heat resistance, commonly used in textiles and mechanical parts.
Poly-methyl methacrylate (PMMA or acrylic) stands out for its optical clarity and weather resistance, making it a popular choice for transparent barriers and signage.
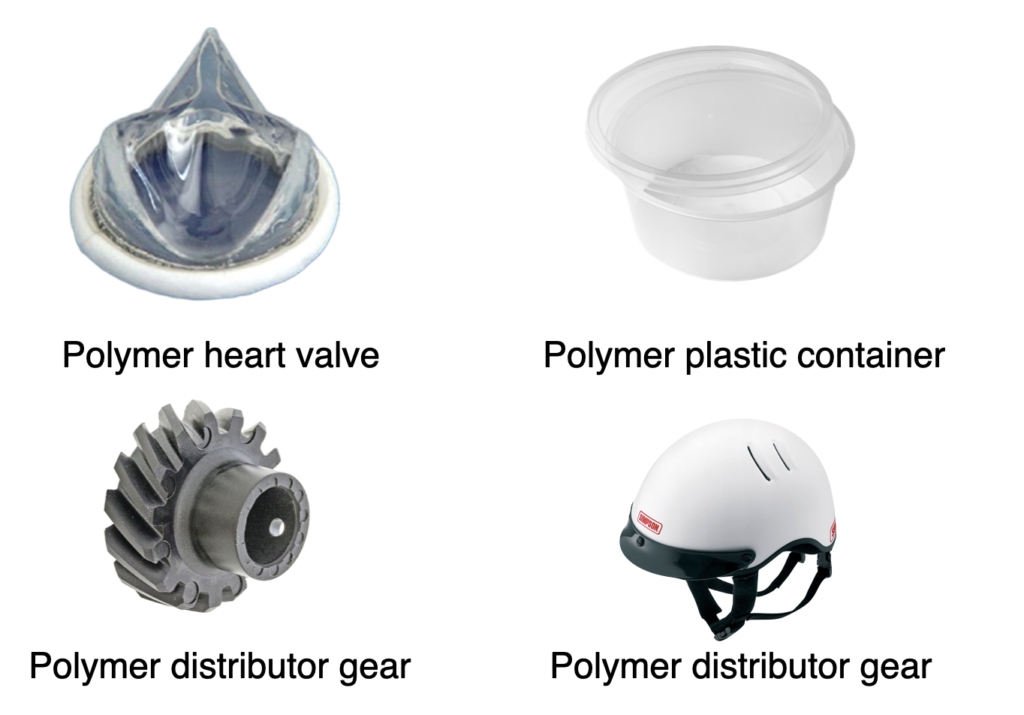
Polyester (PEST) is prized for its high strength, elasticity, and thermal stability, widely used in fibers and films.
Polyvinyl chloride (PVC) is a versatile, chemically resistant, and flame-retardant plastic, extensively used in construction and piping.
Polystyrene (PS) is lightweight, rigid, and an excellent insulator, suitable for packaging and disposable products.
Polytetrafluoroethylene (PTFE) is renowned for its exceptional chemical inertness and non-stick properties, often used in coatings and seals.
Elastomers
Elastomers are a versatile class of polymer materials known for their remarkable elasticity, resilience, and ability to return to their original shape after deformation.
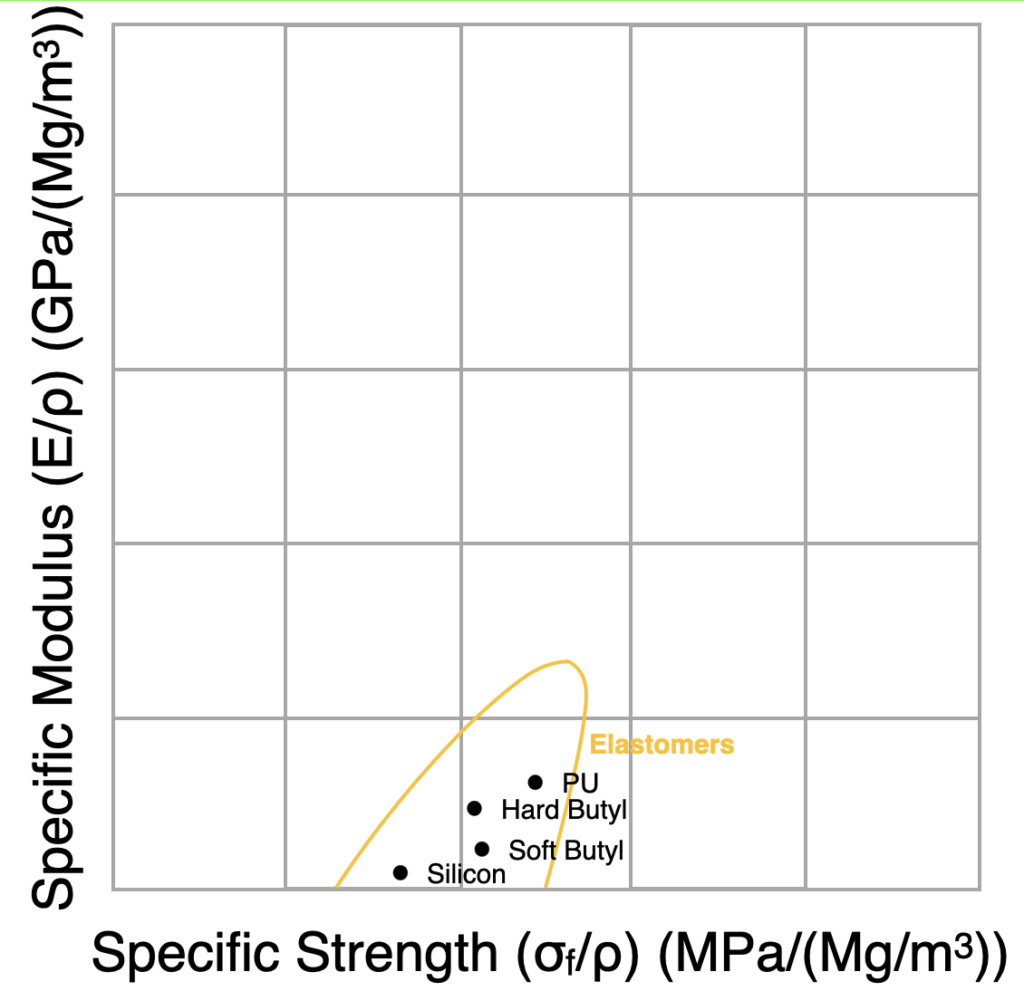
Polyurethane (PU) elastomers are widely used in industrial applications such as rollers, pump liners, machine parts, automotive components, insulation, and even medical devices, thanks to their superior wear resistance, flexibility, and adaptability to various environments.
Butyl rubber, available in hard and soft forms, is prized for its exceptional impermeability to gases, chemical resistance, and excellent damping properties, making it ideal for tire inner tubes, hoses, seals, protective clothing, and vibration dampers in automotive and industrial settings.
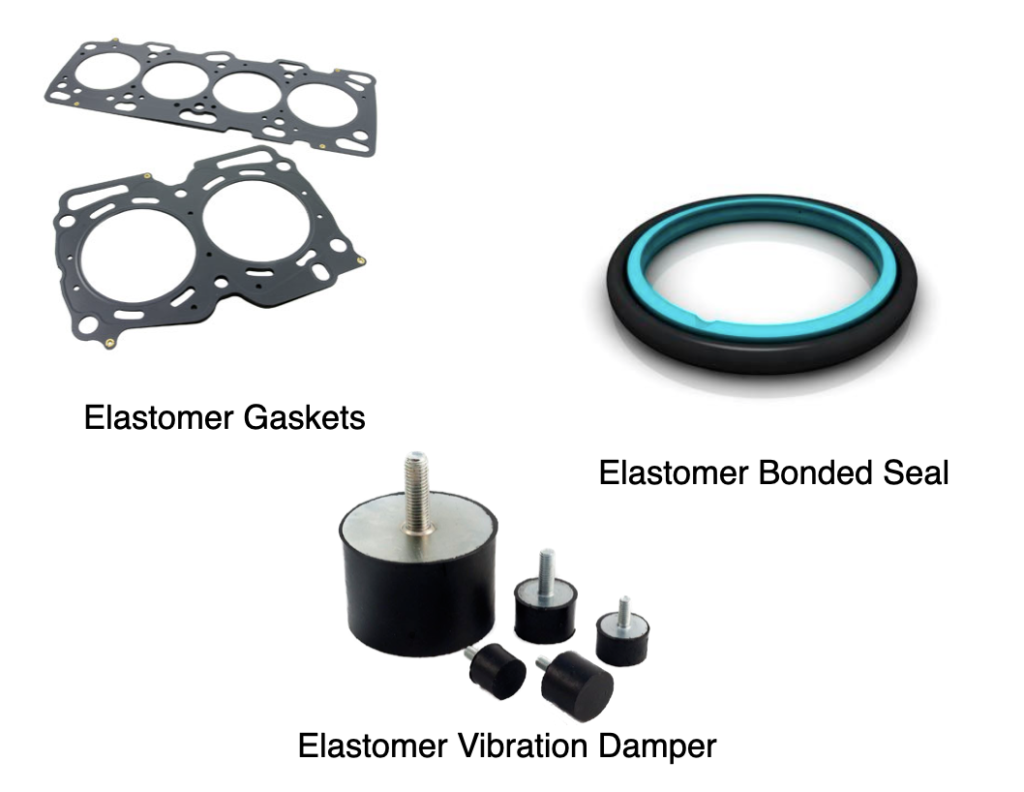
Silicone elastomers stand out for their outstanding electrical insulation, chemical inertness, resistance to extreme temperatures, and biocompatibility, leading to their use in electrical insulation, LED lighting, medical devices, seals, gaskets, and consumer electronics
Highest Specific Properties Materials
Materials with the highest specific properties—meaning excellent performance relative to their weight—include silicon carbide, beryllium oxide, and boron, each offering a unique combination of mechanical, thermal, and electrical characteristics that make them indispensable in advanced engineering applications.
Silicon carbide (SiC) stands out for its extremely high hardness (Mohs 9.2–9.5), high strength, and low density (about 3.2 g/cm³), resulting in an exceptional strength-to-weight ratio. It maintains its mechanical properties at high temperatures, resists chemical attack, and has outstanding thermal conductivity (up to 348 W/m·K), making it ideal for high-performance structural components, abrasives, and heat exchangers.
Beryllium oxide (BeO) is notable for its combination of high specific stiffness, high strength, and low density (about 2.9 g/cm³). It is an excellent electrical insulator but conducts heat better than almost any other non-metal, with thermal conductivity reaching 270 W/m·K, rivaling metals like copper and silver. Its high melting point, chemical stability, and low dielectric loss make BeO a critical material for thermal management in electronics and high-temperature applications.
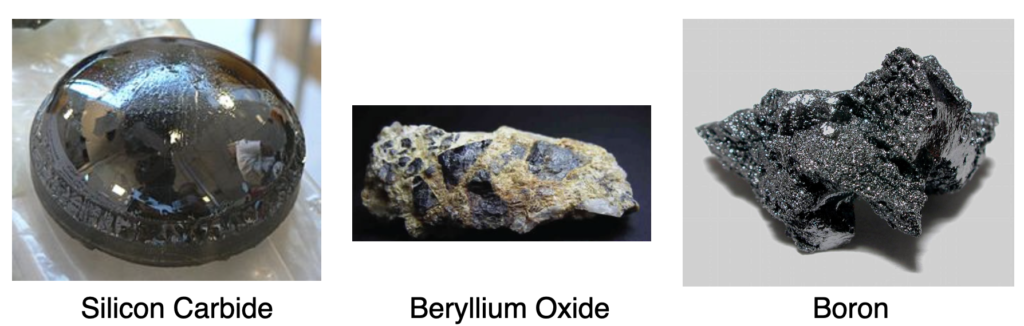
Boron, particularly in its crystalline form, is a lightweight (density around 2.3–2.5 g/cm³) and extremely hard element (Vickers hardness up to 58 GPa), with a high melting point and significant chemical stability. Its high specific stiffness and low density make it valuable for advanced composites, high-strength fibers, and as a reinforcing material in aerospace and defense applications. Boron compounds like boron carbide also exhibit ultra-high hardness and are used in armor and cutting tools
Those materials seems great, but they are also very brittle in Tension
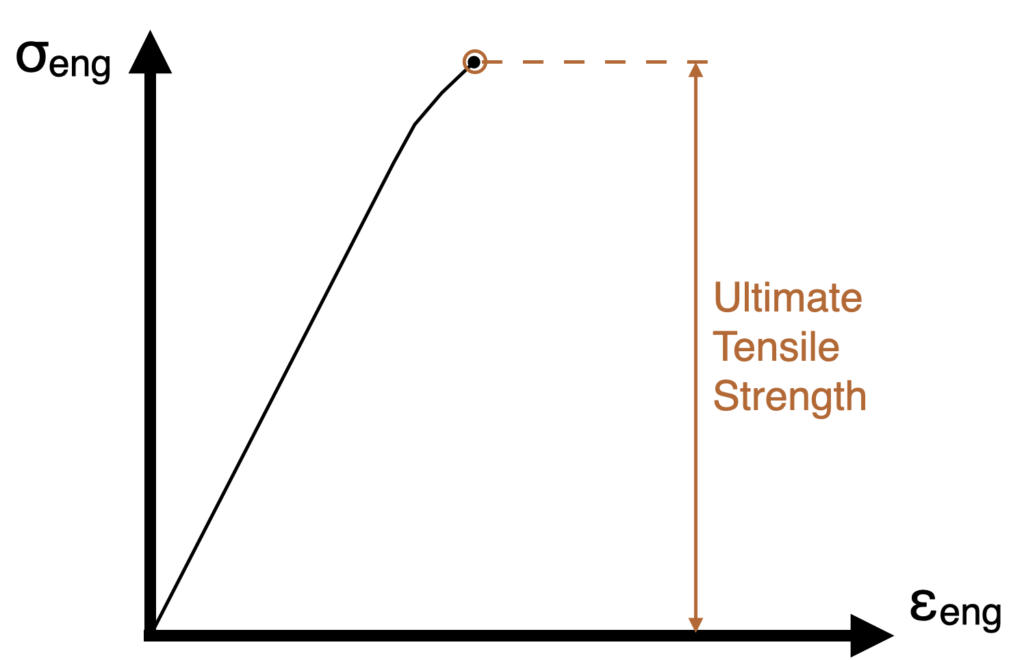
This disqualify them for many applications unfortunately…
Ok, now you must know a lot about composite materials, their strength, their types and applications.
In the next article, i’ll talk more about unidirectional laminates and steel, hoping it will be interesting.
Thanks for reading as always.
Cyprien Rusu
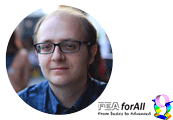
Leave a Reply